Safety in the workplace – how GoatThroat Pumps helps prevent spills and accidents
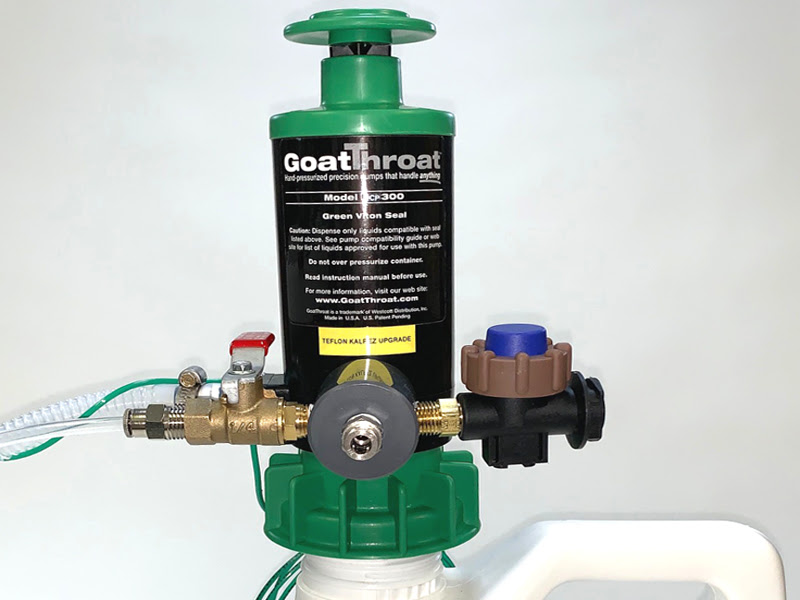
Even in the safest possible working environment, mistakes can happen. And when they involve liquid chemicals, the danger can be very real. Spills can result in injury, property damage, lost productivity and a host of other problems.
Sadly, workplace accidents are all too common in the U.S. The Bureau of Labor Statistics says there were 2.8 million non-fatal workplace injuries and illnesses in 2018. The same year, more than 5,000 Americans lost their life in the workplace.
But it doesn’t have to be that way.
GoatThroat Pumps represents a safer, easier and more efficient way to transfer more than 2,000 types of chemical.
The company uses a sealed system to ensure no dangerous vapors escape. The flow can be controlled precisely – from a drop to a torrent in a matter of seconds. And they work on any container from a two-gallon jug to a 55-gallon drum.
“Safety has always been a major reason why our pumps do so well in a wide variety of workplaces, and why our pumps are now being used in Europe,” says Nancy Westcott, President of GoatThroat Pumps.
The secret is in the delivery system, a manually operated pressure pump that ensures hands are kept well away from danger.
GoatThroat pumps can also be rigged up to a compressor to deliver liquids safely and accurately at the flick of the tap handle. The feeling may be familiar for some. More than a few GoatThroat Pump customers have likened it to tapping a beer keg.
That was the experience of Vincent Francisco, Production Supervisor at Design Mark Industries. “Just pump the plunger a few times, open the spigot and dispense,” he recommends.
“You have full control over how much is dispensed – even the tiniest amounts – or you can leave it open for a continuous flow. It delivers the precise amount needed.”
Design Mark Industries uses flammable chemicals such as acetone in the manufacture of their keypads and touchscreens.
As Production Supervisor, Francisco is responsible for safety. He ruled out tip-and-pour methods due to the risk of injury and lack of precision.
He had tried many manual pumps. But none had lived up to his expectations. Until he used a GoatThroat pump.
“I consider using [GoatThroat] pumps a ‘best practice’ technique because the barrels remain upright and the entire system is sealed so there is never an issue with exposure or VOCs when transferring chemicals,” says Francisco.
He was impressed by their durability too. He estimates that his company has saved thousands of dollars since they started buying GoatThroat Pumps 11 years ago.
“I’ve only replaced one of our three pumps over that time due to constant use, and we could have used it longer,” says Francisco.
When compared to the tip and pour system used across the world, it’s easy to see why GoatThroat Pumps represent a worthwhile investment for so many businesses.
“Protecting employees and businesses from serious accidents and spills is what keeps our engineers working so hard to create the best, user-friendly pumps in the business,” says Nancy Westcott.
“Tip-and-pour is probably one of the biggest culprits for spills. We want to see the end of this dangerous practice in every single industry that continues to use it. Our signature pumps have made the practice obsolete. Recent demand for increased production of disinfection liquids and sanitizers has made safety a priority. And we have the perfect pumps to make the combination of safety and economy a reality.”
Every company wants to ensure their employees are safe at work. Every person working for themselves wants to ensure they are best protected from the perils of the job. GoatThroat Pumps strongly believes that accidents at work and the repercussions that follow are not inevitable. Accidents and spills can and must be prevented.
To find out more about GoatThroat Pumps or to request a media interview, get in touch. https://www.goatthroat.com/about-us/press-media/